How to Tell if a Wall Is Load Bearing
A load bearing wall is responsible for supporting the structural weight of a building. It differs from a non-load bearing wall, often called a ‘curtain wall’ or a 'stud wall', its function is purely to divide rooms, not to carry the building’s weight.
Many buyers viewing properties can be seen tapping walls to measure whether a wall is structural. As a rule of thumb, the sound indicates the hollowness of a wall, it doesn't in any way confirm if a wall is load bearing or not.
How do I tell the difference between a load bearing and non load bearing wall?
Confirming if walls are load bearing falls outside of the scope of work of both the Level 2 and the Level 3 Home Surveys.
These two reports focus on defects in a property. If you intend to confirm if a wall is load bearing, you should speak to a structural engineer. We have a nationwide coverage of structural engineers so you can always contact us to discuss your plans for the property or get a quote.
Fixed Fees | Same week availability* | Access arranged
Visual inspections
- Check for supporting posts, beams, or other walls directly above the wall in question.
- Check the attic or loft - examine if the wall is connected to roof bracing.
- Inspect for supports underneath the wall, such as beams, piers, or jack posts.
- If floor and ceiling joists meet over the wall, it's likely load-bearing.
- Exterior walls are generally load-bearing to support the roof.
Floor plans and structural analysis
- Review the property's floor plan to see if walls on different floors align.
- Buttressing or racking walls may provide horizontal stability.
- If a partial wall has a beam alongside it, it could be load-bearing.
- Thicker walls are often load-bearing.
- Walls in the centre of a structure are more likely to be load-bearing.
- Oriented strand boards (OBS) are often used for structural reinforcement.
What happens if you remove a load-bearing wall?
You must know the location of load bearing walls before carrying out any structural work in a property, such as building an extension. Not doing so makes a potentially life-threatening structural collapse possible.
That is why you must get an experienced structural engineer to inspect the property for you. They will have the necessary knowledge and, in the unlikely event of any damage, structural engineers carry professional indemnity insurance which you will be protected by.
It is a breach of building regulations to remove a load bearing wall without getting it strengthened or having the work signed off and registered at the local authority (council).
On top of this, removing a load-bearing wall yourself without a survey and adequate sign-off, could invalidate your building's insurance.
Walls which are load bearing can be removed, but it is a complex and expensive process which you need a structural engineer to oversee, therefore you should always take professional advice before doing so.
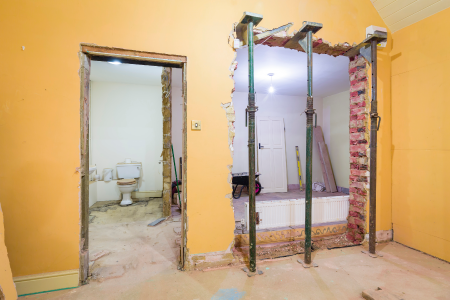
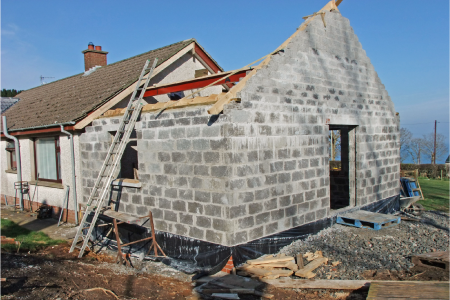
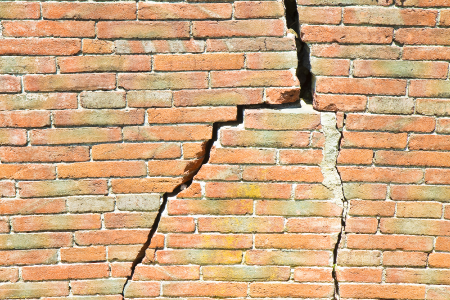
How do you know if you can knock down a wall?
A structural engineer’s inspection for walls which are load bearing will involve an invasive search for structural clues. They will have to access your property’s foundations, look beneath floorboards, and possibly cut into drywall to find supporting beams.
- They start by going to the building’s concrete foundation, the lowest point in the home, and firstly look for walls directly embedded in it: these are load bearing and will, for example, include all four external walls which are all load bearing.
- They then locate the beams. Beams are sturdy pieces of wood which transfer the weight of the building into the foundation. They can go through many floors and therefore be part of many load bearing walls.
- They then work upwards and locate floor joists. These are wooden supporting beams located on the underside of floors and support the rooms above. If they meet a wall or a main support beam at a right angle, they are transferring the weight of the floor above into a wall and therefore, the wall is load bearing.
- They will follow similar procedures to locate internal walls.
A structural engineer can also obtain a building’s blueprints should further research be needed.
Pros and cons of removing a wall
Pros
- Enhanced space and flow: Creating open-plan living areas for a modern and sociable atmosphere.
- Increased natural light: Improving the overall brightness and ambience of your home.
- Architectural flexibility: Adapting your home to changing lifestyles and preferences.
- Potential property value increase: A well-executed wall removal can enhance your home's market value.
Cons
- Structural implications: Removing a load-bearing wall requires careful planning and expert advice to maintain structural integrity.
- Cost: The project can be expensive, including materials, labour, and potential structural reinforcement.
- Disruption: Wall removal and subsequent renovations can be messy and time-consuming.
- Planning permission: You might need planning permission, depending on the nature of the work.
- Unexpected challenges: Discovering hidden issues like electrical wiring or plumbing can add to costs and delays.
Structural engineers will always ensure that any work on load-bearing walls complies with any planning permission or building regulations. SAM's structural engineers carry professional indemnity insurance and are specially trained to comply with local building regulations.
If you're worried about an existing structure in a property you own, we offer a qualifying assessment to confirm whether you're eligible for a Building Control Regularisation Certificate.
Our structural engineer will attend the property to inspect the unauthorised works for compliance with Building Regulations - Part A: Structure.
This is an intrusive survey. The report will:
- Confirm that the works appear compliant and simply need to be signed off by building control.
- Outline any works required to make the work structurally compliant before bringing a building control inspector in to grant the letter of regularisation.
- Confirm that the work would need to be completely undone or redone to meet building regulations.
How to remove a load bearing wall
Important: Removing a load-bearing wall without support can cause structural damage or even collapse.
- Before anything is done, your local Building Control authority needs to be notified of the planned work. It's not essential, but highly recommended that you seek consultation from a structural engineer during this process.
- Before making a hole in the load bearing wall, you have to support ALL the weight of whatever that wall supports by fitting a lintel – often a rolled steel joist (RSJ) bracing the ceiling of the wall. The dimensions of the lintel will be determined by a calculation of the support needed.
- The professional operative drills holes very close to the ceiling and inserts strong steel ‘needles’ at two-foot (61cm) centres across the full width of the opening. The needles must run on either side of the wall by 18 inches (46cm). When these are in place, a timber known as a ‘head tree’ is placed beneath them at each side of the wall. This head tree is normally held up by props at two-foot (61cm) centres.
- With supports in place, the operative cuts the section out for the lintel’s insertion. The opening must be 12 inches (30cm) wider than the opening being made in the wall, to allow the lintel to sit on at least 6 inches (15cm) of masonry on either side of the new opening.
- When the lintel is in place, the masonry can be rebuilt and this may involve forcing in some sand and cement, mortar and even some roofing slate. Once the sand and cement have hardened, the needles and props can be removed and the opening in the wall can be cut, leading to the wall being removed.
- Once all supports are in place and safety is guaranteed, wall demolition can begin and 'making good' can take place.
Load bearing wall removal cost
This task should be handled by someone with the necessary experience and preferably with the guidance of a professional. Many load-bearing walls contain electrical and plumbing components that should be addressed by a qualified professional.
It's advisable to speak with multiple contractors to get quotes on the building work itself.
We can arrange for a structural engineer to advise on your load bearing wall removal. Our load bearing wall survey costs start from £699 INC VAT.
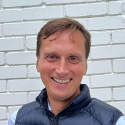
Andrew started his career in 2000 working within conveyancing solicitor firms and grew hands-on knowledge of a wide variety of conveyancing challenges and solutions. After helping in excess of 50,000 clients in his career, he uses all this experience within his article writing for SAM, mainstream media and his self published book How to Buy a House Without Killing Anyone.
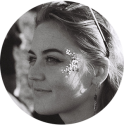
Caragh is an excellent writer and copy editor of books, news articles and editorials. She has written extensively for SAM for a variety of conveyancing, survey, property law and mortgage-related articles.